ClampOn sensors with their high performance filter are unbeatable. The ClampOn Particle monitor with improved filtration of acoustic noise offers unparalleled performance, particularly when monitoring sand in challenging high-pressure, high-temperature (HPHT) conditions.
Using a non-intrusive acoustic sand detector on a HPHT well, one would believe this to be straight forward. After all, measurements are done from the outside of the pipe, hence the pressure does not matter. And while the temperature must be taken into account, it will never pose a major challenge.
ClampOn's experience with HPHT installations over the last 15 years has taught us that it is not quite as simple as one may think.
Around year 2000, ClampOn sand monitoring systems were installed on Chevron Erskin, Shell Shearwater and Statoil Huldra.
Starting up these installations proved several things. Sand monitoring on these installations was considered critical as any sand production under these conditions can be highly dangerous. While sand production was not expected, and certainly not during early production, there was a great deal of focus on the sand monitor readings.
Although sand injection calibration was not possible at the time due to the high pressure, we could see that the high noise levels meant low sensitivity. Until these installations came live, the ClampOn recommendation had been to install the detectors a certain distance upstream of the choke to reduce the effect of choke noise on the readings. Even after doing this however, it was clear that under these conditions choke noise due to the high pressure drop across the choke would still be a challenge.
We initiated a high-priority R&D project to improve noise filtration, and redesigned the calibration tool to allow sand injection at pressures of up to 10 000 PSI. The project was very successful, and in 2005 we solved the challenge of choke noise. ClampOn sand detectors can now be installed downstream of the choke where the velocity is higher and hence the sensitivity is better, and they will not be affected by acoustic noise from the choke. The upgraded sensor, later marketed as the ClampOn DSP-06, was born.
A sand injection was done on the Conoco Jade installation and this clearly demonstrated the significant improvement gained by the improved filter technique.
The first illustration shows the signal from a traditional acoustic detector. Sensor output is at more than 500 000 and the injected sand is not visible.
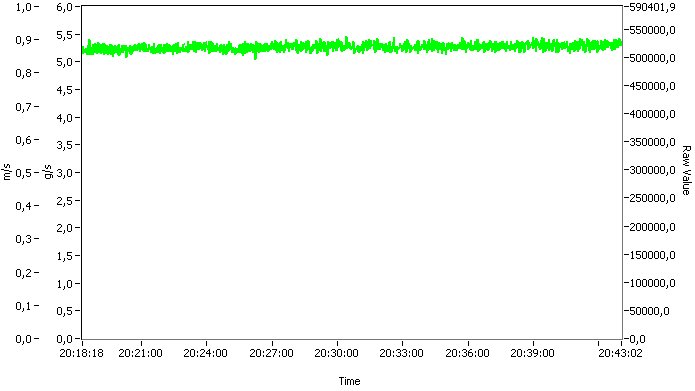
This second illustration
shows the same well and the same injection with the new DSP-06 sensor. Sensor output is now at around 5000 and the injection is clearly visible.
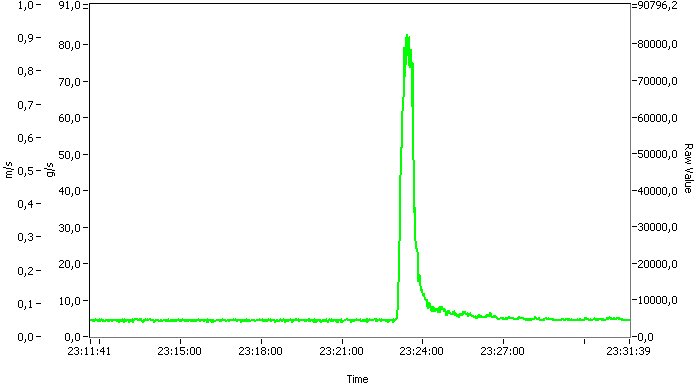
As a result, the systems already installed on the HPHT wells were revisited, and the sensors were upgraded and relocated to a location downstream of the choke.
ClampOn sensors with this high performance filter remain unbeaten. The newer ClampOn Paricle sensor has further improved the filtration, and ClampOn acoustic sand detectors offer unparalleled performance, especially when monitoring sand under difficult HPHT conditions.
ClampOn systems have been chosen for the challenging conditions on Statoil Kristin, Kvitebjørn, and for the new subsea compressor system on Åsgard. For the later installations it has been possible to further improve safety by utilizing the ClampOn Corrosion Erosion monitor and get live, real-time monitoring of wall thickness and erosion.
To strengthen our ability to serve the HP market even more, ClampOn is in the process of building a high pressure sand injection system capable of calibrating the system at flow pressures of up to 15 000 PSI.
More articles
-
Global agents gathered in Bergen
A week of learning, connection, and adventure
-
Subsea Sand and Vibration Monitoring
The project department is bustling with activity as we approach the Easter holiday.
-
Celebrating excellence: Sebastian Skei's top grade in vocational exam
Sebastian Skei achieved an 'Excellent' grade in his six-day vocational exam in Production Electronics
-
Corrosion Monitoring for project in South America
ClampOn have received a large contract for the supply of Subsea Corrosion Erosion Monitoring instruments for a project in South America.