- Home
- |
- Field cases
- |
- ClampOn Choke Condition Monit…
The ClampOn Choke Condition Monitor - how to prevent choke failure
Helping the operator by using ClampOn Choke Condition Monitor to avoid producing with a choke at an opening that can cause high vibration or sound pressure levels
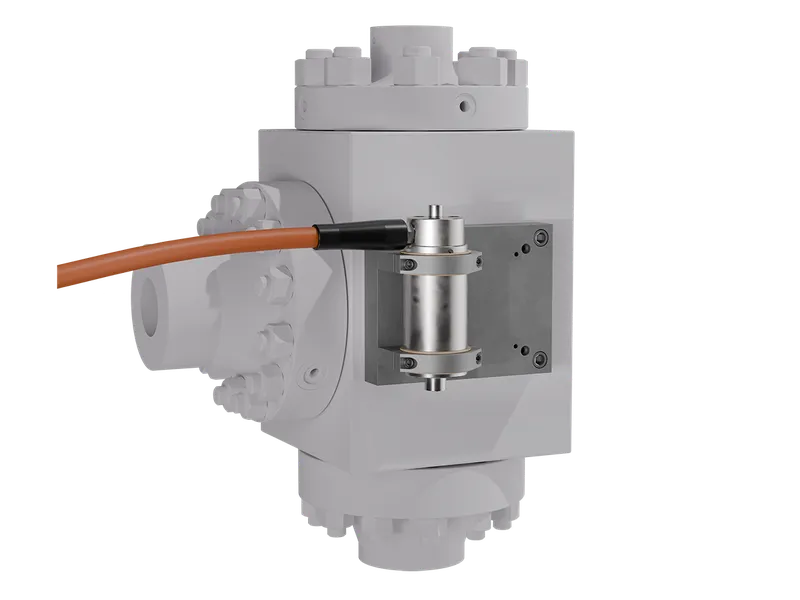
Background
ClampOn was recently contacted by a Norwegian operator, who experienced a choke collapse during the first hours of starting up a new well. They sought assistance in identifying the cause of the collapse and mitigating the risk of future failures. Early investigations suggested that strong vibrations were likely the cause of the collapse. Another potential cause could be the impact of solids or sand; however, the acoustic sand detector did not record any sand production, nor were there any indications of sand downstream of the production system, ruling this out. Material selection was evaluated, considering the combination of high differential pressure (DP) across the choke and potential high vibration.
Subsea choke valve failures can be costly, with component costs, subsea replacement logistics, and lost production time. ClampOn’s Choke Condition Monitor (CCM) can help reduce choke failures by monitoring vibration and acoustic levels, offering operators necessary information to change choke flow and plan maintenance intervals
Challenge
The choke’s failure during the initial start-up procedure aligns with high vibration and/or high sound pressure levels at low choke openings, the latter being the most likely cause. Unfortunately, the acoustic sand detector located a few meters from the choke was not configured to use its onboard vibration monitoring capability, so no vibration data were available for evaluation. The acoustic raw data used for sand calculation showed very high levels prior to and during the failure, not only on the well in question but also on acoustic sand detectors on neighboring wells in the same template.
Example of a worn-out choke insert
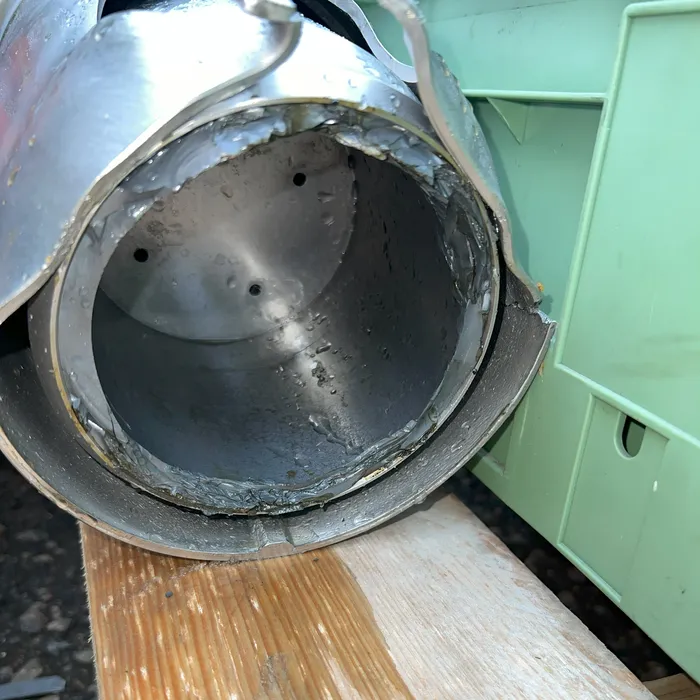
Solution
This indicates a very high sound pressure level at the time of failure. However, it is not possible to quantify the exact level, as the acoustic sand detectors use advanced filtration to remove as much flow noise as possible. Additionally, they are located several meters away from the source, and the noise is transmitted through the water and piping to the instrument. As of the time of writing, four choke failures have occurred, each with different choke trims and materials. One of the risk mitigations implemented was enabling the vibration monitoring capability on the existing acoustic sand detectors and installing the new Choke Condition Monitor directly on the choke body.
Result
This has now been done on one of the wells, which will be operational later this year. This will help the operator avoid producing with a choke at an opening that can cause high vibration or sound pressure levels
Field cases
-
20.06.25
Installation of Subsea Corrosion-Erosion Monitor (CEM) offshore India
Installation and configuration from vessel to seabed
-
02.12.24
The Subsea Corrosion-Erosion Monitor installed from Pipe Laying Vessel
The first installation of the Corrosion-Erosion Monitor onboard a pipe-laying vessel and submerged as a fixed part of the pipeline
-
02.12.24
ClampOn Corrosion-Erosion Monitor for integrity monitoring of buried pipes
The instrument was installed underground with cabling to a cabinet with solar power and radio telemetry.