A new in-house flow loop brings new opportunities for ClampOn.
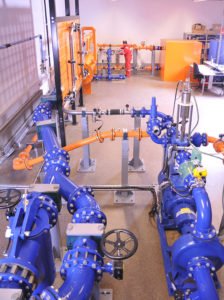
A new in-house flow rig brings new opportunities for ClampOn. "Our new flow loop greatly improves our service, research, and development capabilities," says Tormod Reigstad, Systems Engineer, who has been responsible for the flow loop project.
Construction started about a year ago, with the rig taking up most of the 100 m2 test room in the basement of ClampOn's headquarters. The loop consists of two sections: one primarily for air, supporting a velocity of up to 40 m/s; the other primarily for water with a velocity of up to 15 m/s.
Injectors add a controlled amount of particles to the air or water, which is then lead through a construction made specifically for testing purposes. Pipe size and configuration can be altered, and sensors can be installed in different locations to test various flow scenarios.
After testing, a filter makes sure HSE requirements are met by separating the particles from the air or water to ensure the safety of the operators.
Previously, ClampOn had to do air system testing externally. Arild Bakke, Senior Mechanical Developer Engineer, points out that being able to perform such tests in-house will cut down on development costs and provide instant verification of theoretical results, helping make ClampOn’s product lines even better.
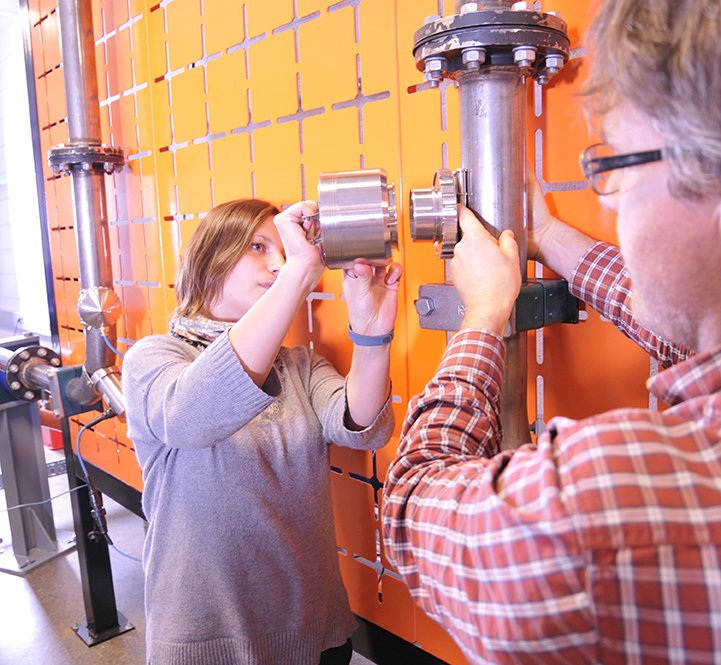
The service department will also benefit from the new equipment, and training of internal and external users will be easier. The flow loop will provide data to better understand operating windows for ClampOn's acoustic sensors, i.e. operating limits regarding small particles, low flow speeds, and different liquid/gas conditions.
"A better understanding of the optimal window for sand injection calibration will help us determine when a new calibration is needed, and when the calibration used for one well can be used for another. We have a lot of data already, but more testing and reconstruction of different scenarios will help us confirm our theories," says Torbjørn Haugsdal, Service Manager.
The flow loop can also provide special services for ClampOn's customers, for example product demonstrations. Haugsdal's team has also performed specially requested tests, for instance using specific particle types such as Dolomite and proppants.
"Of course, there are other flow loops that have different capabilities than ours. However, the ClampOn flow loop can be mobilised on short notice and tests can be performed with quick and accurate results," says Haugsdal.
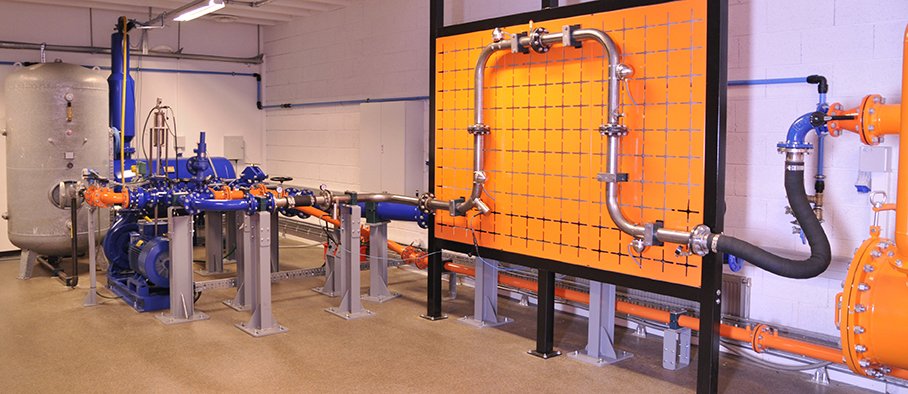
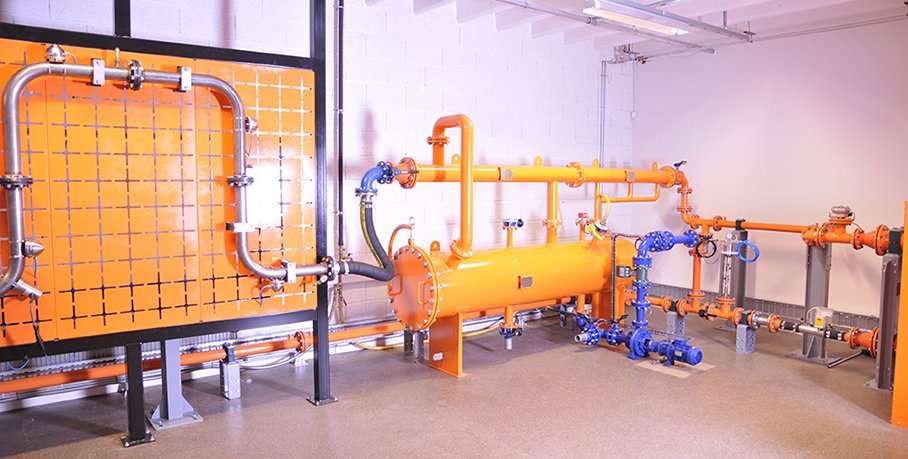
More articles
-
Global agents gathered in Bergen
A week of learning, connection, and adventure
-
Subsea Sand and Vibration Monitoring
The project department is bustling with activity as we approach the Easter holiday.
-
Celebrating excellence: Sebastian Skei's top grade in vocational exam
Sebastian Skei achieved an 'Excellent' grade in his six-day vocational exam in Production Electronics
-
Corrosion Monitoring for project in South America
ClampOn have received a large contract for the supply of Subsea Corrosion Erosion Monitoring instruments for a project in South America.